穴あけ加工とは?方法・種類・用途
切削加工の1つで木材や鉄板、アルミ板やステンレス板などの代表的な加工方法でもある穴あけ加工。それぞれの素材にあった工具や切削方法を見極めることが大切です。本記事では木材や鉄板、アルミ板や難削材であるステンレス板に至るまでの切削方法や注意点を紹介しています。
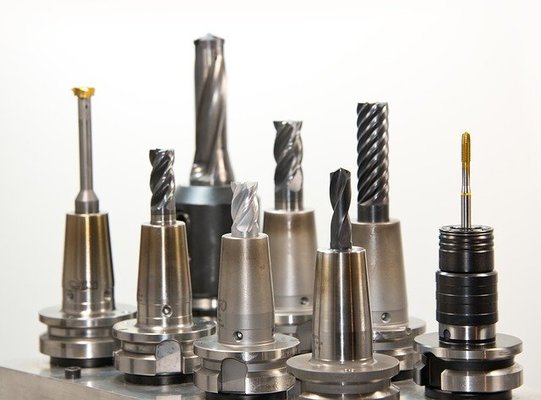
目次
穴あけ加工とは?
穴あけ加工とは、ドリルで素材に穴をあける加工方法です。ドリルを使用するため、ドリリングとも呼ばれます。穴あけ加工は切削加工の1つで、穴のない機械部品はないと言っていい程に、機械加工の中で最も使われている加工方法です。
金属だけではなく、木材やプラスチックに加工を施すこともあります。また、大工や職人がノミやかんなで木材を削るのも切削加工です。素材を加工するという意味では、料理の際の皮むきも切削加工に入ります。
一口に穴あけ加工といっても様々な種類があり、母材の材質やどのような穴をあけるかによって適切な方法や工具を選ぶ必要があります。穴に合わせた工具や加工方法の選択を誤ると、素材や工具を無駄にしたり、工数が増え時間も無駄にしてしまいます。
穴あけ加工を含む切削加工には以下のメリットがあります。
- 自由な形状のものを作りやすい
- 精度が高いものが作れる
反対に、デメリットとして以下のことが挙げられます。
- 大量生産に向いていない
- 材料を削りながら作り上げていくためロスが出る
工業製品の小型化・高機能化・軽量化に伴い、穴あけ加工はより細分化を求められるようになっています。加工する材料に高精度で効率的に穴あけ加工ができる技術の進歩が必要です。
穴あけ加工の方法
穴あけ加工で、主に使用される工具は以下の3つです。
- ボール盤
- ドリル
- リーマ
素材を固定するテーブルの役割をするボール盤、穴を開けるためのドリル、開けた穴の精度を調整するリーマです。ボール盤に固定した素材に対して、回転するドリルを垂直に下すことで真っ直ぐな穴をあけます。最近ではマシニングセンタと呼ばれる工具自動交換機能を備えた機械を使用し、自動で穴あけ加工されることも珍しくありません。
穴あけ加工の種類
穴をあけるといっても必要に応じた切削方法があり、使い分けが必要になってきます。穴あけ加工の中でも代表的な5種類について詳しく解説します。
- 浅穴加工
- 深穴加工
- ソリッドドリリング加工
- トレパニング加工
- カウンターボウリング
浅穴加工
浅穴加工とは、ドリル直径の3倍以下の長さの穴をあける加工方法です。木材に浅穴加工をするときは、ビットと呼ばれる工具で手回しで行うこともあります。
深穴加工
深穴加工とは、ドリル直径の10倍を超える穴をあける加工方法です。
深穴を高精度で仕上げるには、特殊な機械と技術が必要になります。深穴用のドリルは全長と溝長が長く、通常のドリルと比べて折れやすくなっているため、振れに注意をして切り屑の排出にも気をつけましょう。
深穴加工をするときは高精度な前加工と切削条件を決めておくのが良いとされています。前加工とは、位置決め、同型のガイド穴をあけるといった処理です。
ソリッドドリリング加工
ソリッドドリリング加工は、主に未加工の状態の材料に穴をあける際に用いられる加工方法です。浅穴加工で最も使用されている方法で、無垢穴加工とも呼ばれています。ソリッドリリングで深穴加工を行う場合は、深穴用に作られた深穴用ロングドリルを使用します。
トレパニング加工
トレパニング加工は、主に大径の穴加工に用いられており、円筒状に切削をすることでソリッドドリリング加工と比べるとより少ない動力で穴をあけることができ、深い穴にも対応可能です。
穴の中心には円柱状のコアが残り、高価な素材を切削する場合などはコアを再利用できるというメリットがあります。そのため、貫通穴向けの加工方法と言えます。
カウンターボウリング
すでにある穴を大きくしていく加工方法です。
下穴をあけてからカウンターボーリング加工をすることで、仕上がり面の精度調整や加工精度が求められる場面で使用されます。また機械の動力が限られている場合、先にソリッドドリリング加工で小さな径で穴をあけてからカウンターボーリングを行うことで、必要としている穴の径までもっていくことが可能です。
シンニングによる加工・形状・用途
シンニング加工とは、ドリルの心厚部(剛性を持たせるため、ドリル中心部に設けられているウェブという部品の先端部の厚さ)に切れ刃を形成する研磨のことです。シンニング加工をするメリットは以下の3点です。
- スラスト抵抗を減らせる
- 切り屑の排出性能が向上する
- 工具の寿命が延びる
スラスト抵抗を減らせる
ドリル先端の中心部分にある刃(チゼルエッジ)は、穴あけ加工の最初に素材に触れる部分ですが切削能力がありません。切削中のチゼルエッジは素材を押しつぶすかたちとなり、スラスト抵抗(ドリルの軸方向にかかる抵抗)の半分以上を持っています。
そこでシンニング加工を行い、チゼルエッジの長さを小さくすると、素材への刃の通りがよくなり、切削抵抗を軽減できます。
切り屑の排出性能が向上する
チゼルエッジの長さが小さくなるとすくい角の面を広くとれるため、切り屑を排出できる部分を大きくとれます。それにより切り屑の排出もスムーズになるため、切削効率が上がります。
工具の寿命が伸びる
上記の2点によりドリルにかかる負荷が減るため、結果的にドリルの寿命は長くなる傾向にあります。シンニング加工は形を組み合わせたり、再研磨の際に形状を変えたりして、より効率的に穴あけ加工をできるようになるのです。
X形
X形は心厚が大きなドリルに用いられることが多く、スラスト荷重を大幅に減らすことが可能です。シンニングを施す前と比べると刃の食いつきが良くなります。用途としては、木材や鉄板、アルミ板などの一般加工や深穴加工で使われることが多くなっています。
XR形
X形に比べると素材への食いつきは劣ります。特徴として切れ刃の強度が高く、使用できる素材の適用範囲が広く長寿命なことがあげられます。X形と同じく木材や鉄板、アルミ板などの一般加工で使用されますが、特性を生かしてステンレス板などの粘り気のある金属への穴あけ加工にも使用されます。
S形
S形は研削が簡単にできるので、最も一般的なシンニング加工と言われています。再研磨も比較的簡単で、低心厚や先端角の小さいドリルに対して有効な加工方法です。鉄板、鋼や鋳鉄、ステンレス板、アルミ板等の非鉄金属の一般加工に使用されます。
N形
心厚が大きいドリルに用いられることが多く、チゼルエッジの周りの切り屑ポケットが大きくなるため、排出性に優れています。N形も低心厚や先端角の小さいドリルに対して有効な加工方法です。そのため、深穴加工に使用されます。ステンレス板で使用されることもあります。
ドリルによる加工・形状・用途
金属加工用のドリルは、ツイストドリルです。半世紀以上前に発明されたものが改良を加えられて今でも使用されています。また、通常金属加工用ドリルは先端の角度が90度または120度になっています。
穴あけ加工は、プレス加工などに比べると作業スピードが遅いため、小ロット生産に向いていると言えます。仕上がりはバリやカエリが出やすいので、リーマ加工などで精度を調整するのに時間がかかります。そのため、短い納期には適していません。
ボール盤を使用するドリル加工は、プレス加工に比べると穴がずれたり穴の径にバラつきが出やすくなっています。ドリルの柄の部分(シャンク)の形状によりストレートドリルとテーパードリルに分けられます。
ストレートドリル
正式にはストレートシャンクドリルと呼びます。シャンクとボディの直径サイズが同じ大きさのドリルのことで材質を問わず、一般的な加工で使われています。
ストレートドリルは直径13 mm以下が通常で、ボール盤などのチャックは直径13 mmまでしか固定できないものがあるので注意が必要です。13mmを超えると切削時に振れが出ることがあり、精度が落ちてしまう傾向にあります。
テーパードリル
正式にはテーパーシャンクドリルと言われており、標準品で径75mmまでのドリルがあります。
テーパードリルのメリットは、ドリルの振れに対する精度があがること、取り付けや取り外しが簡単なこと、高負荷に強いことがあげられます。そのため13mmを越えるドリルは穴あけ加工だけではなく、フライス加工や旋盤加工の際に使用されることもあるのです。
上記を踏まえ以下に4つの素材の穴あけ加工についてのポイントを解説しています。
木材
木材に穴あけ加工をする時は木材用のドリルビットを使用しましょう。木材用のドリルビットには貫通穴用と止まり穴用があります。木材に釘やビスを打ち込む際は小さいものでないかぎり、下穴は開けたほうが無難と言えます。下穴を開けておくと木材にドリルを差し込んだ時に食い込みがよくなります。特に木材の端に穴をあける際には、木材が割れてしまう危険がありますので下穴は必須です。
鉄板
鉄板の穴あけ加工には鉄工用のドリルを使用します。金属加工における「一般的」とは鉄を指しています。鉄板に限ったことではありませんが、金属で最初から大きい穴をあけると抵抗が大きく時間がかかってしまいます。下穴をあけておく、切削油を差すといったことで解決が可能です。出来上がった穴にはバリがあるのでリーマ加工などで取り除きましょう。
アルミ板
アルミ板金属の中では柔らかい部類に入るため、穴あけやその他の加工がしやすくなっています。その反面、加工後には必ずバリが出るため処理が必要です。切削にはシャープな切れ刃と、広い切りくず排出面を持つ工具が適しています。アルミ板は高速切削が基本です。切削時の摩擦熱で歪みやすいためクーラントなどを使用した対策をしましょう。
ステンレス板
上記3つと比べるとステンレス板は、穴あけ加工をするのが難しい素材と言えます。熱伝導率が低く加工硬化率が高いことが影響しています。ステンレス板に穴を開ける時はステンレスドリルかコバルトドリルを使用しましょう。
鉄板用のドリルでも穴あけは可能ですが、ステンレス板は熱伝導率が悪く、ドリルに熱がこもってしまい、ドリルが焼き付いてまったく切れなくなってしまいます。そのため鉄板用のドリルを使用すると、ドリルの交換頻度とドリルの購入費用が高くなります。また、ステンレス板用のドリルを使用するよりも時間がかかり、効率的ではありません。
以上のことから、ステンレス板にはステンレス用のドリルを使用する事が望ましいです。
穴あけ加工の注意点
穴あけ加工を行う上での注意点は以下4点です。それぞれについて解説します。
- 油量と油圧を適切に調整
- 切削条件
- 熱変形に注意すること
- ケガや事故に注意
1.油量と油圧を適切に調整
穴あけ加工の際は切り屑が次々に生成されます。切削油またはエンジンオイルを注油することにより、スムーズに切り屑が排出されるようになります。ただし、切削油量も計算して必要量を算出してから使用する必要があります。1分間に必要な切削油量はドリルの直径に比例しています。
例えば10mmのドリルで1分間の穴あけ加工を行うとすると、10リットルの切削油が必要となります。必要な切削油の量は作業前に計算しておきましょう。
2.切削条件
素材の材質や硬さ、形状、工作機械の性能や特性を見極めて工具を選び、どれくらいの速度でどのくらいの精度の穴をあけたいのかを考慮する必要があります。加工速度が速すぎると、切削熱と素材との抵抗にさらされますのでドリルの寿命は短くなります。回転数が遅くてもビビりや振動でドリルの寿命が縮むことがあります。
また精度も落ちてバリやカエリが出てきたり、リーマ加工などで後処理をしっかりとしなければなりません。工数が増え、時間もかかってしまうので適切な加工速度で効率的に作業を進めるようにしましょう。
3.熱変形に注意すること
穴あけ加工はドリルが回転しながら素材に触れることで切削していきますが、同時に熱が発生します。この熱により、素材や工具が熱変形を起こすことがあります。削る速度が速いほど摩擦が激しくなるため、高温の熱が発生しやすく、さらに素材の面積が大きいと熱変形が生じやすくなっています。切削油やエンジンオイルを使用して、工具と素材を熱を冷ましながら作業をしてください。
また、加工に時間がかかるとわかっている場合は定期的に休憩をして、工具も素材も人もリフレッシュしてから作業にあたると生産性も上がります。
4.ケガや事故に注意
穴をあけるだけと、油断をしていると大きなケガや事故につながります。高回転のドリルから発生する切り屑が目に飛んでくることも考えられますので保護メガネをするなどの対策をしましょう。また、穴あけ加工に限ったことではありませんが、回転する工具を取り扱う時は巻き込み防止のため、軍手をしないなどの徹底が必要です。
作業をする場所や使用する機械や工具についての安全ガイドやマニュアルを遵守し、ケガや事故を未然に防ぎましょう。
まとめ
本記事では穴あけ加工について解説しました。事前に素材や加工方法や工具を正しく選定し、効率よく作業をすすめることが必須となります。最近ではステンレス板などの難削材の使用により加工が難しくなっており、さらに納期も短くなるなど、全てを自身で賄うのは難しくなっているのが現状です。自分で穴あけ加工を行うのが難しい場合は、専門の業者に外注するのも1つの方法です。
【穴あけ加工の種類】
- 浅穴加工
- 深穴加工
- ソリッドドリリング加工
- トレパニング加工
- カウンターボウリング
【穴あけ加工の注意点】
- 油量と油圧を適切に調整
- 切削条件
- 熱変形に注意すること
- ケガや事故に注意