深絞り加工とは?種類・工程・製品例・注意点を分かりやすく解説!
本記事では、深絞り加工の定義、加工方法の種類、実施工程や注意点について解説します。深絞り加工はシンプルな構造で大量生産に適していますが、精度や品質向上のための設計コストが高いのが弱点です。特徴を把握して、高品質な製品を製造しましょう。
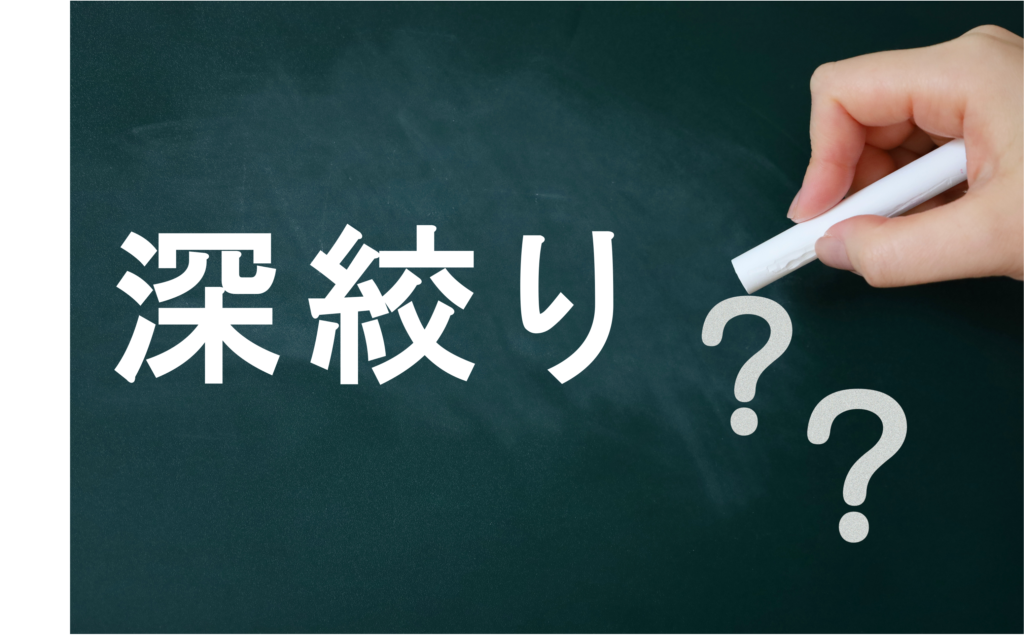
目次
深絞り加工について、お調べでしょうか。
深絞り加工はシンプルな構造の加工法で、少ない工程で成形ができます。
大量生産に適していますが、精度や品質向上のための設計コストが高いのが弱点です。
不確かな技術で設計すれば、品質の悪い粗悪品を大量製造してしまう危険も。
そこで本記事では、深絞り加工の定義、加工方法の種類、実施工程や注意点について解説します。
深絞り加工の特徴を把握して、高品質な製品を製造しましょう。
深絞り加工とは?
深絞り加工とは、金属板成形法の一つです。
金属の薄板を円筒・角筒・円錐など、さまざまな形状の底付容器に加工できます。
加工方法の特徴を知らなければ、目的の製品に適した方法か判断ができません。
知識をつけることで、自分の目的とする加工が可能かどうか判断できるようになります。
深絞り加工の定義や用例を理解して、加工方法の選定に役立てましょう。
円板から円筒容器を作る加工【直径<深さ】
深絞り加工は、円盤から円筒容器を作る加工です。
絞り加工の中でも、仕上がった製品の直径に対して、深さの方が長いものが深絞り加工です。
対して、深さの方が直径よりも短いものが浅絞り加工になります。
直径と深さを比較した上で、深いものを深絞りと覚えておきましょう。
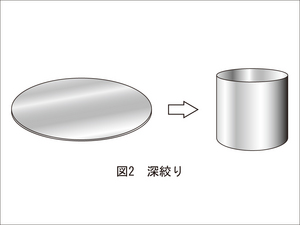
深絞り加工の仕組み
深絞り加工の仕組みはシンプルです。
成形したい形の凹みをもつ下側の金型(ダイス)と、そこに沈み込む上側の金型(ポンチ)がペアになり、一枚の板に圧力を加えて成形します。
深絞り加工は、金型で圧を加えて成形する、シンプルな構造の加工法です。
深絞り加工がされる製品例
深絞り加工では、金属の薄板から加工するので、円筒・角筒・円すいなど、つなぎ目のないさまざまな底付容器の加工が可能です。
具体的には、キャップ類、風呂容器、アルミ缶、エンジンカバーなどの加工に用いられています。
つなぎ目の無い容器形状の加工には、深絞り加工が適切です。
深絞り加工の種類【形状別6種類】
深絞り加工はシンプルな構造で、さまざまな底つき容器の成形に用いられる加工法です。
深絞り加工の製法は、目的とする形状別で6種類に分類されています。
種類を知れば、希望の加工が可能です。
希望の加工ができるようになれば、目的の製品を確実に作ることができます。
1つずつ、見ていきましょう。
円筒絞り加工
円筒絞り加工は、円筒状で底つきのある容器を形成する手法になります。
真ん中が空洞になった上下の金型に金属を挟み、パンチの打ち込みで圧をかけて成形する塑性加工です。
主に、フライパンや鍋といった製品の加工に用いられています。
円筒状の底つき形状の成形には、円筒絞り加工が適切です。
角筒絞り加工
角筒絞り加工は、角筒状の底つき容器を制作する際に有用です。
角筒絞り加工は、角部分と辺部分が違う動きをするため、円筒絞り加工よりも難易度の高い加工方法となります。
キッチンシンクのような形状の製品を成形する際に、適した加工法です。
異形絞り加工
異形絞り加工は、自動車の車体パネルなどの複雑な形状を作るための加工法です。
異形絞り加工では、深絞りと曲げの2工程で複雑な形状を実現します。
単純に二つの加工を行うだけで製品が出来るわけではなく、形状に合わせて材料にかかる応力の設計が必要です。
異形絞り加工は、複雑な形状が加工可能な一方で、設計難易度が要求される加工法になります。
円錐絞り加工
円錐絞り加工は、タンブラーなどの円錐形製品に用いる方法です。
円錐系では、金属板を回転させながら、へらと呼ばれる棒を押し当てて加工します。
手動あるいは、マシニング制御で加工しますが、へらの操作に技術が必要な加工法です。
円錐絞り加工は、テーパードのかかった錐形を成形できる方法ですが、構造が他の絞り加工よりも複雑で技術の求められる加工法になります。
角錐絞り加工
角錐絞り加工も、側面がテーパー状になっている容器を形成する手法になります。
円錐加工と異なり、錐の側面が平面な形状になることが特徴です。
円錐よりは加工が容易ですが、テーパードのかかった錐形状に加工するため、他のプレス加工よりも技術が求められます。
角錐絞り加工は、角錐形状の部品加工に用いれられる加工法です。
球頭絞り加工
球頭絞り加工は、容器の底が半球状となっている容器を形成する手法です。
球頭絞り加工をする時は、半球形のパンチや液圧で成形します。
半球形状の製品ができるので、調理用ボウルなどの制作で用いられる加工法です。
ダイスにはめ込まないため、張り出し加工とも呼ばれます。
深絞り加工の工程を6ステップで紹介!
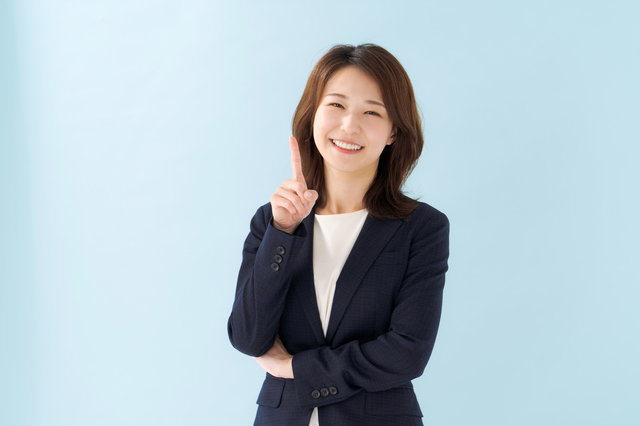
深絞り加工で、加工できる形状についてはご理解いただけたでしょうか。
ここからは、深絞り加工の工程と設計基準をステップで紹介します。
工程と設計基準を事前に把握すれば、工程から逆算したスムーズな設計作業が可能です。
工程を1つずつ見ていきましょう。
ステップ1.ブランク形状と寸法の決定
最初の工程は、ブランク形状と寸法の決定です。
ブランクとは、素材となる板を指します。
まず、ブランクを絞り加工して形状を変えていきますが、1回に絞れる径には限界があるため、最初に絞る「初絞り」の後に、「再絞り」が続くことを念頭に置いた設計が必要です。
ブランクの直径に必要な値は、フランジと絞り部分の直径、更に絞り部分の高さと3つです。
ブランク直径の計算は、以下の式によって算出されます。
D=√(d^2+4dh)
d:フランジ直径 d:絞り部分の直径 h:絞り部分の高さ
最後に絞ったフランジのトリミングを行って完成です。
ステップ2.絞り工程数の決定
ブランクの寸法を決定したら、次は絞り工程数の検討です。
絞り率を基準に1回あたりの搾り径を計算して、絞り工程数を決定します。
絞り率の計算は、以下の計算式によって算出しましょう。
絞り率(m)=絞り後の径÷絞り前の径
工程ごとの絞り率は以下が目安です。
初絞り…m1=0.5~0.6
2絞り…m2=0.75~0.8
3絞り…M3=0.8~0.9
工程が繰り返される毎に、加工硬化の作用で絞りにくくなることを覚えておきましょう。
ステップ3.金型設計
工程数計算の後は、金型設計です。
絞り加工ではダイスとパンチ、2種類の金型設計が必要になります。
ダイスの金型設計は、パンチがダイスの中に入り込んだ時のすき間を基準に直径を算出します。
またフランジの幅に合わせて、押さえ台の幅の設定も必要です。
押さえ台の設計が甘いと、フランジ部成形時にしわに繋がります。
パンチの設計には、パンチの直径と肩半径の算出が必要です。
肩半径の算出には、工程数に応じて変形を加味した設計が必要なので、試行錯誤が求められます。
ステップ4.プレス機械の選定
プレス機械は算出された絞り加工力を基準に、トルク出力を満たすものを選定します。
絞り加工力は、以下の式で算出しましょう。
絞り加工力(P)=K・n・d・t・Ts(kgf)
K:係数 n:円周率 d:絞り径 t:板厚 Ts:引っ張り強さ
絞り係数のKは、相対板厚という板の厚みを基準に算出されます。
相対板厚=板厚÷ブランク直径×100(%)
(最大値1.0)
ステップ5.絞り材料の選定
プレス機の選定後は、絞り材料の選定をします。
絞り材料は、加工の対象となる材料です。
選定は、以下のr値、n値を基準に実施します。
名称 | 定義 | 特徴 |
r値 | 引き伸ばしたときに板厚方向よりも幅方向に縮みやすい材料であるかどうかを示す数値 | r値が大きいほど絞りやすい |
n値 | 加工硬化係数。 加工したり変形させたりすることで材料が硬くなる性質を表す値 | n値が大きいほど硬くなる |
r値が高いほど絞り加工に適しており、n値が高ければ張り出し加工向きの材料です。
必要な値は素材や、加工形状によっても異なります。
r値やn値が高い素材であるほど、加工難易度は高いです。
目的に合わせた適切な絞り材料の選択をすれば、加工に対する金型の負荷も減ります。
適切な材料選択は、コスト削減に繋がるのです。
ステップ6.潤滑油の選定
絞り材料が決まったら、使用する潤滑油の選定です。
潤滑油には、油性タイプと水性タイプの二種類があります。
以下で、表にまとめましたので見ていきましょう。
分類 | 利点 | 弱点 |
油性タイプ | 汎用性が高く、安価。防錆性を付与できる。 | 温度の影響をうけやすく熱がこもりやすい。油なので作業環境を汚しやすい。 |
水性タイプ | 冷却性が高く、摩擦熱を冷却可能なので高速生産に向く。 | 錆びのリスクがある。 |
錆びにくい金属で高速生産を行いたい場合は、冷却性能が高い水性タイプが有利です。
その他の用途であれば、安価で汎用性が高い油性潤滑液が推奨されます。
材料の性質、高速生産を求めるかなどの条件用途に応じて潤滑油の選定をしましょう。
気をつけて!深絞り加工の注意点
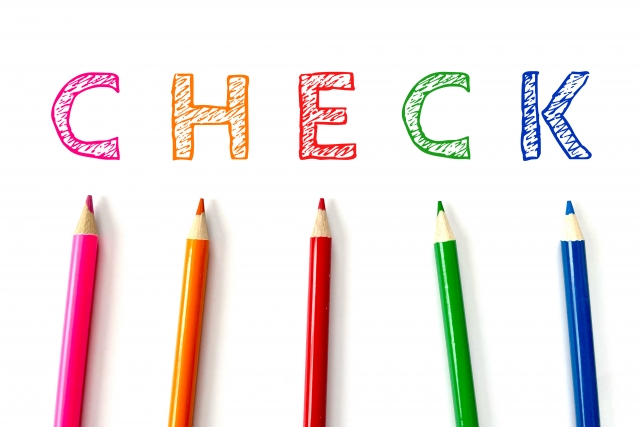
深絞り加工は、シンプルな加工方法で量産に適しています。
一方で、設計には緻密な計算が必要です。
技術と経験に基づいた正確な設計ができなければ、粗悪品の量産にも繋がりかねません。
ここからは、設計を行う上での注意点を紹介します。
注意点を理解して、高品質の量産が可能な金型設計を成功させましょう。
仕組みはシンプルだが技術が必要【金型・機械・加工条件】
シンプルな仕組みの深絞り加工ですが、高品質な製品を量産するには技術が必要です。
設計が甘ければ、成形品にしわや割れのリスクが発生します。
たとえば限界絞り比、加工時や局部への負荷設計ミスは、底、フランジ、側面などに割れが発生するリスクの要因です。
また、パンチとダイスの摩擦や金属材料の選定にミスがあると、しわの発生原因となります。
経験や、技術にもとづいた知識がなければ、割れやしわが発生する金型を設計してしまうリスクもあるのです。
もし、絞り加工で割れやしわといった欠陥が生じる場合には、金属材料を変更したり、プレス加工の条件を変更して改善ができます。
しかし、改めて設計と金型の成形をすれば余計に費用がかかってしまいます。
設計に不安がある場合は、技術のある専門業者への依頼も検討してみましょう。
深絞り加工にお困りなら鋼の専門商社に相談!
深絞り加工の設計と実施に自信がない人は、プロへの依頼も検討しましょう。
設計と加工のプロである鋼材専門業者であれば、経験豊富な技術を元に精度の高い加工対応が可能です。
こちらでは、クマガイ特殊鋼株式会社について紹介します。
クマガイ特殊鋼株式会社
クマガイ特殊鋼株式会社は100年以上の歴史があり、深絞り加工に対する経験や知識も豊富です。
業界の長い歴史で培われた基盤と幅広い知識を元に、鋼材加工に対応可能な知識と技術を有しています。
目的にあった素材の選定や、精度の高い設計に自信がない場合はクマガイ特殊鋼株式会社に相談しましょう。

まとめ
深絞り加工は、成形したい形の凹みをもつ金型(ダイス)と、パンチで一枚の板に圧力を加えて成形する方法です。
シンプルな仕組みなので、加工工数が少なく、品質が安定しやすい利点があります。
一方で、金型の設計には緻密な計算が必要で、質の悪い金型では割れやしわのある欠陥品が製造されるというリスクもあるのです。
もし、深絞り加工にお困りの場合は、実績多数の専門商社クマガイ特殊鋼株式会社までお問い合わせください。
深絞り加工について、プロとして親身に相談に乗ります。