円筒研削とは?利点欠点から仕組みまで分かりやすく解説
円筒研削は、高い精度が特徴の研削方法になります。しかし、精度が高いという利点があるという一方で、生産性に劣ることが欠点です。 本記事では、円筒研削の仕組みからポイント、欠陥と対策まで解説しています。円筒研削の正しい知識をつけて、最高の製品を作りましょう!
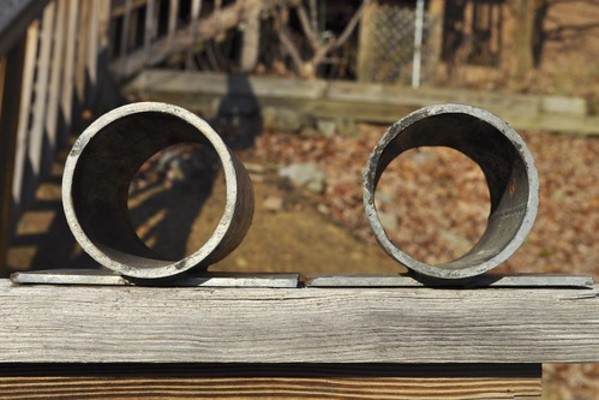
目次
円筒研削についてお調べでしょうか。
円筒研削は、高い精度が特徴の研削方法になります。
しかし、精度が高いという利点があるという一方で、生産性に劣ることが欠点です。
そこで本記事では、円筒研削の仕組みからポイント、欠陥と対策まで解説しています。
本記事を読めば、円筒研削の構造や、加工を成功させるために意識すべきポイントの理解が可能です。
円筒研削の正しい知識をつけて、最高の製品を作りましょう!
円筒研削とは?【円筒状工作物の外面を研ぐ】
円筒研削は、円筒状の工作物の外面を研削する加工法です。
工作物は両端のセンタで支持され、旋盤の場合と同様に回転運動が与えられます。
まずは、円筒研削の特徴と、加工に適した製造物を紹介しますので見ていきましょう。
寸法精度や面粗さを要求されるローラー・シャフトに適した研削方法
円筒研削は、ローラーにより研削を行う加工法です。
表面の研磨ができるため、凹凸のない面粗さの高さを要求される製造に適した加工法になります。
また機械で研削を行うため、寸法精度も高いです。
円筒研削は寸法精度、面粗さを高いレベルで実現できる特徴からローラー・シャフト類の研削に適した研削方法です。
円筒研削の利点と欠点【心なし研削との比較】
円筒研削は、面粗さが高く寸法精度が高いことが特徴ですが、利点や欠点も存在しています。
利点と欠点を知れば、利点を活かした加工と欠点を考慮した計画が可能です。
それでは、見ていきましょう。
利点
円筒研削の利点は2つあります。
- 芯なし研削に比べて精度が高い
- 溝などがあっても加工可能
利点を理解すれば、どんな製造物に円筒研削が最適なのか理解が可能です。
詳細を説明します。
心なし研削に比べて精度が良い
(出典:株式会社酒井鉄工所)
円筒研削は、心なし研削に比べて精度が良いです。
心なし研削では、加工対象を調整車と砥石と研削用の砥石で挟んで研削を行います。
円筒研削では、加工対象の横軸を固定した状態で研削を行うため工作物の安定感から加工精度に優位です。
工作物を横軸で固定して研削する、円筒研削は心梨研削に比べて加工精度が高くなります。
溝などがあっても加工可能
円筒研削は、溝などがあっても加工可能です。
心なし研削では、交差物の場合溝が固定の弊害となり加工ができません。
一方横軸に固定箇所を置く円筒研削では、工作物に溝があっても研削ができます。
円筒研削は、心なし研削で加工できない溝のある工作物も加工可能です。
欠点
精度の高さと、溝がある工作物にも対応できる汎用性をもつ円筒研削にも欠点はあります。
以下で詳細を見ていきましょう。
生産性に劣る
生産性に劣ることは、円筒研削の欠点です。
円筒研削は加工の工程で、製品の着脱や機械操作の時間が必要になります。
加工の工程上、どうしても生産あたりに時間がかかるのです。
円筒研削は生産性に劣るため、大量生産に不向きであることが欠点となります。
【画像あり】円筒研削の仕組み
円筒研削の利点と欠点につづいて、次は円筒研削の仕組みを紹介します。
加工の仕組みを知れば、目的の工作物を作るために適した工法なのか高い精度で判断可能です。
砥石による研削を行う円筒研削には、下記の3つの加工法があります。
- トラバース研削
- プランジ研削
- アンギュラ研削
それぞれの仕組みを見ていきましょう。
トラバース研削
(引用:遠州工業株式会社)
トラーバース研削は、工作物を横軸方向に移動させながら研削する加工法です。
工作物を軸方向に往復させることで、平面を加工できるのが強味になります。
また、軸方向の往復研磨により加工後の面粗さが高いため鏡面加工も可能です。
トラバース研削は、工作物を横軸方向に移動させ面粗さの優位な研削方法になります。
プランジ研削
(引用:遠州工業株式会社)
プランジ研削は、工作物を固定して砥石を動かして研削する加工法です。
横軸方向の移動があるトラーバース研削より力が強く伝わるため、能率的な研削ができます。
能率性が高い研削により、工作機械への負担が少ない加工が可能です。
プランジ研削は、工作物を固定して行う能率性が高い研削方法となります。
アンギュラ研削
(引用:TechNote)
コマ型の砥石を工作物にあてる方法を、アンギュラ研削といいます。
アンギュラ加工はコマの形状から、通常円筒研削ではできない端面に凹を作れることが強味です。
またコマ状の砥石から、外径だけでなく側面の一括加工なので側面加工を要する際は生産性においても優位といえます。
アンギュラ加工は、コマ状の砥石により外径の凹加工や側面加工が可能な研削方法です。
押さえておこう!円筒研削のポイント
円筒研削では、工作物を横軸に動かすトラバース研削、工作物を固定して研削するプランジ研削、コマ状の砥石を用いるアンギュラ研削があることは理解いただけたと思います。
それぞれに特徴はありますが、総じて研削による加工精度が求められる要素です。
円筒研削では、ポイントを押さえた加工方法をすることで精度向上ができます。
本記事では、そんな円筒研削の加工の際のポイントを紹介です。
スパークアウトすることで一層の精度向上を図れる
円筒研削では、スパークアウトすることで加工精度を向上できます。
スパークアウトとは、工作物と砥石をゼロ距離で空転させるテクニックです。
切込を入れず、ゼロ距離で空転させることで工作物の外径周辺の切り残しが除去できます。
円筒研削では、最後の仕上げにスパークアウトを用いることで一層の精度向上が図れるのです。
気をつけて!円筒研削で起こり得る欠陥と対策
円筒研削では、スパークアウトポイントで精度向上を図れます。
一方で、加工の際には抑えるべき注意点もあります。
注意点を理解しない加工を行えば、欠陥製造の原因ともなり得るのです。
円筒研削で起こる欠陥は以下の3つになります。
- びびり
- きず・送りマーク
- ワーク精度不良
それでは見ていきましょう。
びびり
びびりとは、加工対象の仕上げ面に発生する斑模様のことです。
機械の振動、振れや砥石の精度不良、加工条件の不適合、切れ味の低下などが原因で発生することがあります。
以下の表に、びびりの原因と対策をまとめたので見ていきましょう。
現象 | 原因 | 対策 |
びびり一般 | 砥石の目直し不良 | 鋭いドレッサで目直しする。 |
一定の広い間隔の変色したびびりマーク | 砥石選択の不適当 | 粗い粒度or 軟らかい結合度or 粗い組織の砥石を使用する。(目つぶれ・目づまりの可能性大) |
長くて広い間隔のびびりマーク | 駆動ギヤのバックラッシュ | 古いギヤの場合は取り替え。 V ベルトを使用する。 潤滑油に異常がないか調べる。 |
不規則なびびりマーク | センターor センター穴の不適 | センターのはまり方を調節する。 潤滑油を注ぐ。 |
レストの不適合 | レストのあたり具合を調節する。 |
円筒研削で発生するびびりの原因は、砥石の不良や、センターの調整ミスなど様々な原因が要因となって発生します。
事前の確認はもちろんですが、もし発生した際はびびりの模様から原因を分析し、適切な対策を行いましょう。
きず・送りマーク
円筒研削では、きずや送りマークも発生しやすい欠陥です。
きずや送りマークも、びびりと同様にそれぞれに考えられる原因があります。
以下で原因と対策を表にまとめました。
現象 | 原因 | 対策 |
幅が狭くて深い一定のきず | 砥石選択の不適当 | 細かい粒度の砥石を使用する。 |
不規則な幅広いきず | 砥石選択の不適当 | 結合度の硬い砥石を使用する。 |
孤立した深いきず | 砥石の目直し不良 | 鋭いドレッサで目直しする。 |
ドレス後砥石面を研削液できれいにする。 | 研削液の不適当 | 有機質結合剤に対して強すぎるアルカリ性の研削液を使用した場合、ソーダを減らすか研削液をかえる。 |
ネジ状の送りマーク | 粒度の選択が不適当 | 粗仕上にもっと細かい粒度を、仕上には比較的粗い粒度を使い、砥石の切込と送りを次第に小さくし、スパークアウトまで行う。 |
砥石の周速度が不適当 | 砥石周速度を遅くする | |
センター合わせ不良 | センターの芯合わせor砥石軸とワークの芯合わせの点検をする。 | |
目直しが不適当 | ドレッシング切込と送りを小さくする。 |
きずや送りマークの欠陥の際は、砥石の選択ミスだけでなく研削液の選択ミスなども疑われます。
幅の狭さや、不規則さなどに合わせて砥石の粒度や結合度の硬さを検討しましょう。
ワーク精度不良
最後の欠陥はワークの精度不良です。
研削の対象であるワークの精度が、目的とするレベルに達していなかった際は欠陥となります。
ワークの精度不良について原因と対策を表で見ていきましょう。
現象 | 原因 | 対策 |
ワークの真円度不良 | 砥石選択の不適当 | 軟らかい結合度の砥石を使用する。 |
ワークの不平衡 | ワークのバランスをとる。 | |
ドレッシング不良 | 研削位置とドレス位置を適合させる。 | |
センターorセンターレストブレードの不適当 | センター穴を正しくあける。 センター穴を修正研削し、ラッピングする。 センターとセンター穴に注油を十分行う。 |
|
ワークの円筒度不良 | 砥石選択の不適当 | 硬い結合度の砥石を使用する。 |
研削盤の調整不良 | 磨耗部分の修理・交換。 両センターの位置修正。 |
|
ドレッシング不適当 | 研削位置とドレス位置を適合させる。 | |
ワークの熱膨張 | 研削液を多量に注ぐ。 砥石の切込量や送りを調整する。 |
ワーク精度の不良は、ワークのセッティングミスなどによって発生します。
その他、真円度不良がある際は柔らかめの砥石、円筒度に不良がある際は硬めの砥石を選択するなど砥石の検討も重要です。
円筒研削にお困りの場合は鋼の専門商社へ相談もアリ!
円筒研削にお困りの場合は、プロへの依頼も検討しましょう。
設計と加工のプロである鋼材専門業者ならば、経験豊富な技術を元に精度の高い加工対応が可能です。
クマガイ特殊鋼株式会社
クマガイ特殊鋼株式会社は100年以上の歴史があり、円筒研削に対する経験や知識も豊富です。
業界の長い歴史で培われた基盤と幅広い知識を元に、鋼材加工に対応可能な素材知識と加工技術を有しています。
対象となる素材に合わせた最適な加工設計、素材に合わせた工具の選定、機材のセッティングに自信がない場合はクマガイ特殊鋼株式会社に相談しましょう。
まとめ
円筒研削とは、円筒状の工作物の外面を研削する加工です。
工作物は両端のセンタで支持され、旋盤の場合と同様に回転運動が与えられます。
研削の中でも、寸法精度や面粗さを要求されるローラー・シャフトに適した研削方法です。
精度が高いという利点がある一方で、機材セッティングの工程が必要なため生産性は劣るという欠点もあります。
また、加工の際の機材セッティングが製品の品質に影響するため、高い品質を保つには知識と技術が必要です。
万が一、円筒研削についてお困りの際はクマガイ特殊鋼までお気軽にご相談ください。
鋼のプロとしてきめ細かいサポートをお約束します。