型彫り放電加工とは?メリットやデメリット、原理を解説
型彫り放電加工とは油等の絶縁性がある加工液のなかで電極とワークを向かい合わせ、微小な放電を繰り返し発生させることによって加工する放電加工です。本記事では型彫り放電加工がどんなものなのか用途や原理についてと、メリットとデメリットを解説します。
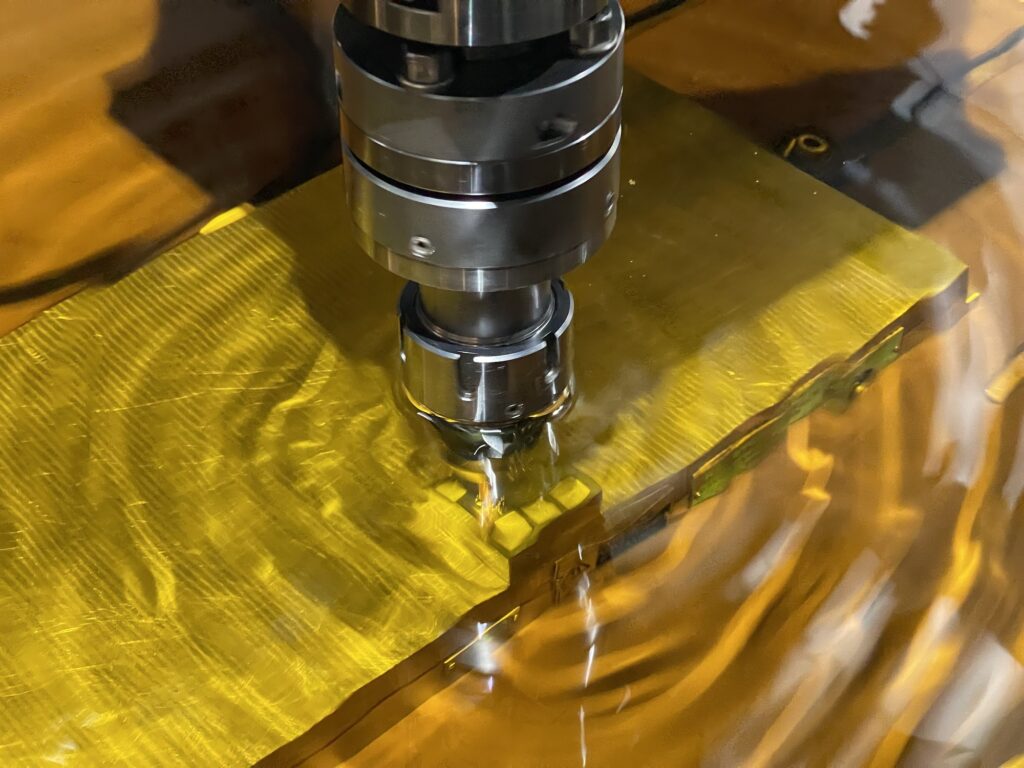
目次
放電加工とは?
放電加工とは水や石油などの加工液の中で電極とワークを向かい合わせ、その間で発生した電気エネルギーで火花を起こし、その熱によって金属をとかして加工する方法です。
加工液の中で火花を発生させると、金属の溶けた場所が加工液によって急激に冷やされ、気化する際の圧力で溶接した箇所を吹き飛ばしながら除去します。
金属の残った部分は月のクレーターのような形にくぼみます。放電加工は、こうした火花を断続的に飛ばして金属を熔解し、冷却させて飛散することを繰り返しながら金属を加工する方法です。
さまざまな加工法の中でも放電加工が優れている最大の理由には、硬度の高い材料に対して、複雑な形状の精密加工ができることです。放電加工によって、通常の切削加工では不可能な焼入れ材のように硬い金属でも穴を開けたり溝を掘ったり、精密な形状に加工できます。
近年では、硬い金属への小さな穴開け加工にも放電加工が用いられています。また、加工品質も良く、工具が破損するリスクも少ないため、スリット加工にも使われています。
ただ、放電加工は切削加工と比べると、加工速度が遅いという欠点もあるのですが、この比較は切削加工でも可能な、硬度が高くない金属加工での比較です。硬度の高い材料では切削加工では難しいため、正しい比較はできません。
放電加工は工具電極を用いることによって、形状を反転させた加工をすることができます。また、工具電極にワイヤを使うことで、板状の金属を糸鋸状に加工することが可能で、精度の高い2次元加工が可能です。
放電加工の仕組み
放電の身近な例といえば、静電気があります。冬の乾燥した日など、金属のドアノブに触ると、バチッと衝撃を受けることがありますが、これは衣服などを通して身体に溜まった電荷が放電するためです。
また蛍光灯の光も放電によって発光していますが、これらは気体の中での放電です。一方、放電加工は液体の中での放電です。放電加工は、加工液の中で必要な穴直径よりも小さな直径の電極を使って、かなり硬い金属でも加工を行うことができます。
加工用に使用される電源は直流ではなくパルス電源を使いますが、放電が発生する距離で放電が連続して発生して終了します。この後も少しだけ電極を材料に近づけることで、再び放電が連続で発生します。
こうした動作を続けることで、電極の直径よりもわずかに大きな直径の穴が、対象の材料に加工されていきます。これが液中放電加工の仕組みです。使用する加工液には、絶縁性の高い灯油系の加工油や、イオンを取り除いた水が用いられます。
灯油の中で火花を発生させるため、爆発や火災が起こらないのか心配する人もいるかもしれませんが、液中の底の方で火花放電があっても、周囲には酸素はなく爆発や火災が起こることはありません。ただし加工液の表面近くで火花放電があれば、大気中の酸素と反応する可能性があります。その場合は火災の恐れがあるため、注意する必要があります。
加工液の中で放電すると、気化爆発を起こして気泡が生じます。この気泡の爆発によって、溶け出した材料を吹き飛ばし、小さなクレーター状の窪みを生成しますが、これが放電加工の基本原理です。
このクレーターのことを放電痕といい、1回のパルス放電によって形成されるので、放電加工における加工単位となります。1秒間に数千回ものパルス放電が発生し、それを数分から長い加工になると数十時間も連続して加工を行います。対象の材料には、電極形状を反転した凹凸が形成され、放電加工された加工面を顕微鏡などで観察すると、小さな放電痕が連なりデコボコの状態であることが分かります。
放電加工の種類
放電加工の種類には大きく分けて、以下の2つの種類に分けることができますが、それぞれについて解説します。
・ワイヤー放電加工
・型彫り放電加工
ワイヤ放電加工(ワイヤー放電加工)
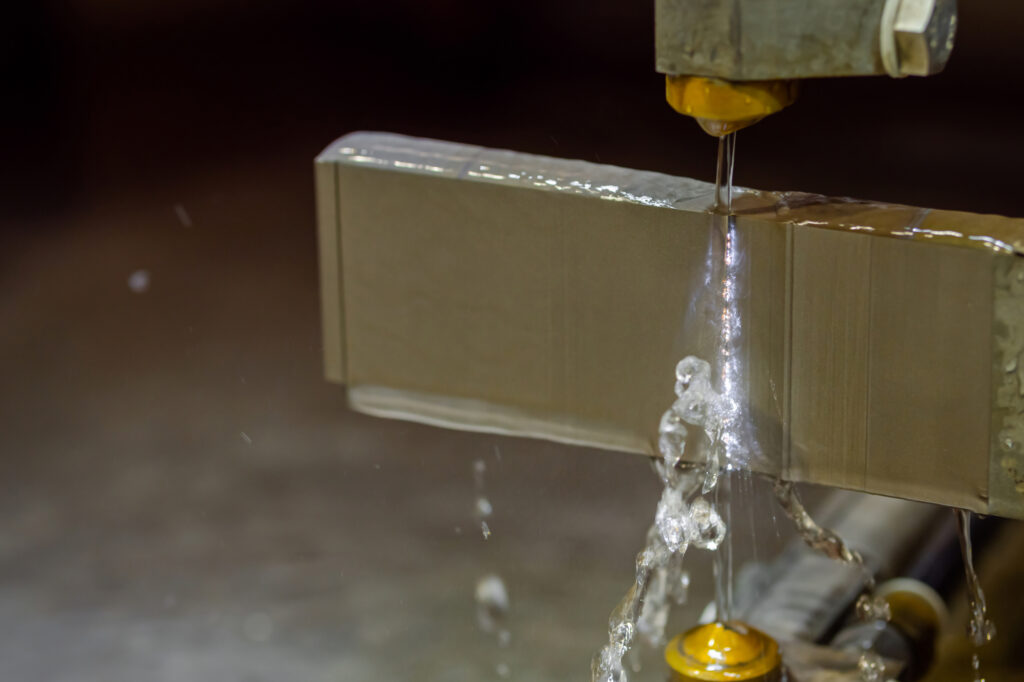
ワイヤー放電加工を分かりやすく説明するとワイヤーを放電させたときに発生する熱によって目的の材料を加工する技術です。熱による加工法には他にレーザー加工があります。レーザー加工は光の熱を利用しますが、ワイヤー放電加工では電気エネルギーの熱によって加工します。
ワイヤー放電加工の仕組みはワイヤーとワーク(加工するもの)の距離を近づけていくとワイヤーとワークが実際に接触していなくてもワイヤーとワークの間隙には電子の通り道ができています。
このワイヤーとワークの間に発生した通路は電気抵抗性が高く高温と光を発生しながら電気が流れます。その高温を利用して加工する技術がワイヤー放電加工です。
ワイヤー放電加工では、ブロック材の加工などに用いられますが、その他に金属板の切断や穴あけといったものによく使われています。ワイヤー放電加工に利用される金属の材質は、鉄・ステンレス・銅・アルミ・真鍮などがあげられます。
形彫り放電加工
型彫り放電加工とは、加工する材料を電極の形状に応じて加工する技術です。一般的に削ることが難しい材料の加工に適しています。
型彫り放電加工は、彫りたい形に加工された電極を対象の材料に近づけて放電させ1秒間に1000から10万回火花を飛ばすことで、材料を少しずつ溶かし理想の形に加工していきます。
また電極が材料に触れることなく、一連の作業は加工液のなかで行われます。電極と材料との隙間は、わずか0.005~1.0mmでこの隙間を「放電ギャップ」と呼びます。電極にはグラスファイトやタングステンなど、電気を通しやすい物質が使用されますが、電極は簡単に加工することが可能な柔らかい金属を使用することが特徴です。
放電加工のため、加工対象となる材料も電気を通す素材でないといけませんが硬度に関係なく加工することが可能です。
形彫り放電加工とワイヤー放電加工との違い
形彫り放電加工とワイヤー放電加工は、以下の3つの違いがあります。それぞれについて解説します。
- 電極の違い
- 加工の仕方の違い
- 主な加工物の違い
電極の違い
型彫り放電加工の電極は、材料に加工したいものを転写した形状ですが、ワイヤー放電加工では、電極は細い糸状のワイヤーです。
加工の仕方の違い
型彫り放電加工での加工の仕方は、掘っていくイメージで貫通させない加工もできますが、ワイヤー放電加工では、糸鋸で切るようなイメージで貫通させて加工します。
型彫り放電加工機は樹脂金型(インジェクションモールド)などの凹凸状に加工し、ワイヤ放電加工機は抜き金型のパンチ形状やダイ形状に加工します。
主な加工物の違い
型彫り放電加工の主な加工物は金型ですが、ワイヤー放電加工の主な加工物は金型と刃先加工です。
型彫り放電加工とは?
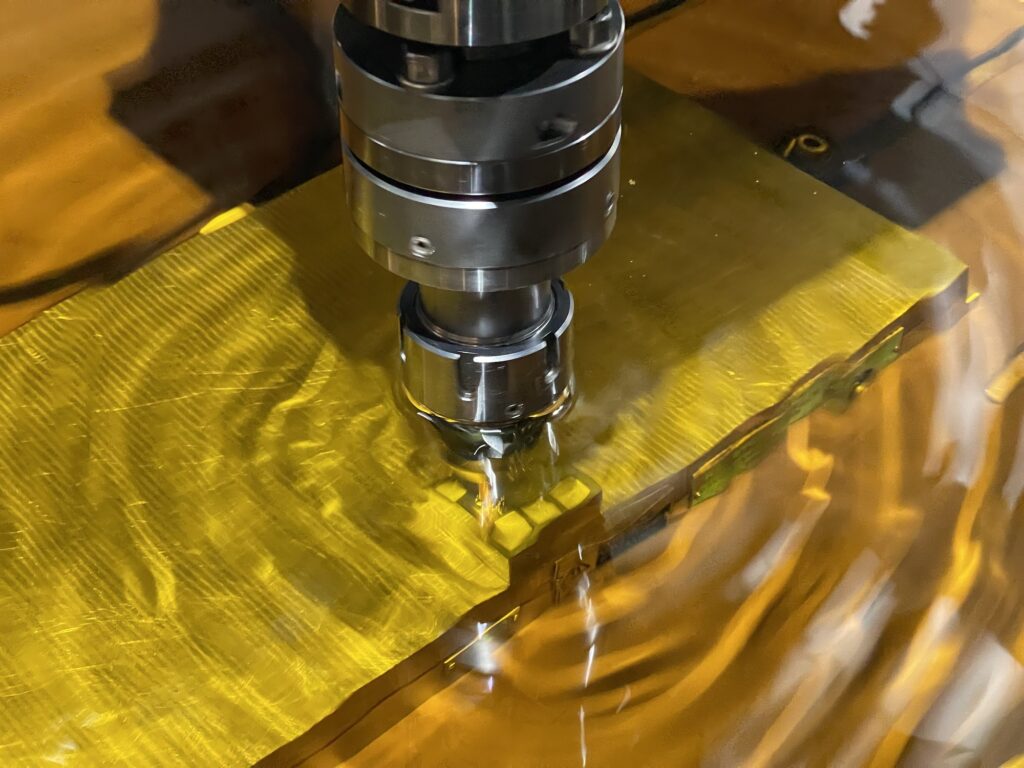
型彫り放電加工とはは油等の絶縁性がある加工液のなかで、電極と材料を向かい合わせ、微小な放電を何度も発生させて放電加工させる技術です。型彫り放電加工は、放電熱によって材料の一部を溶接し加工液の中で発生する気泡の爆発によって溶接箇所を飛散させて排除します。
このように加工液のなかの細かい除去を繰り返しおこなうことで電極形状が、反転された3次元形状に加工することが可能です。そのため銅・タングステングラファイトなどの材料に加工し電極を作る必要があります。
また電極に角がある場合加工物の仕上げ形が崩れてしまうこともあります。そのため、高い精度で仕上げるためには、電極を2個用意し、加工途中でも新品に替えるなどの工夫も必要です。
型彫り放電加工の用途
型彫り放電加工は、電極に銅やグラスファイトなどを使用し形状を転写する放電加工で通電性がない材料には、適用できません。通電性があれば超硬材や焼入材など硬度に無関係に加工が可能です。
ワイヤーカット放電と異なる点は貫通させなくていいことや底付などのポケット加工や、電極次第では色々な形状の転写ができることです。
型彫り放電加工の用途はマイクロレベルの微細な加工、ロケットエンジン・ノズルスカートのような大型加工まで加工することが可能です。たとえば、携帯やスマホ、最先端の航空機、宇宙ロケットに使われる工業製品など、これらを製造するために金属材料の精密形状加工が大切です。
放電加工は部品自体だけでなく部品を製造する金型の仕上げとして使用されることもあります。放電加工は、金属を精密加工する方法の1つでもあります。
型彫り放電加工の原理
型彫り放電加工は、加工液に加工する対象材料を沈め、加工形状を反転させた形の電極を作ります。電極と加工する対象材料の間に電気によって火花を飛ばし、その熱で溶かすことによって加工します。
型彫り放電加工機の構造と特徴
型彫り放電加工機は形状加工された電極を使って、電極が反転した形の工作物を加工しますが加工機の構造は、C型コラム形状が通常です。電極を取り付ける主軸と材料を設置するXYテーブル、加工用の電源装置、加工液を溜める工槽、各軸を制御するNC装置で構成されています。
各軸とも一般的にボールネジを使ったサーボモータで制御を行います。近年は応答性を高めたリニアモータが用いられることがあります。またどちらのモータもマイクロメートルの移動や位置を決めることができます。
加工槽は数百リットルの加工液を溜めることができ、加工液は常に循環させ加工粉などの不純物を濾過しています。また加工液には油系加工液が使用されますが、火災の心配があるため、温度検知センサーを装備した自動消火装置の取付けが必須です。
電極材料は銅やグラファイトを使いますが加工精度や加工速度の向上が目的です。
銅材やグラファイト材の電極材料は丸や四角など一般的なものが販売されています。また希望する加工形状が市販の電極形状と違う場合切削加工によって、電極の形状に整形しなくてはならず余分な工程がかかってしまいます。
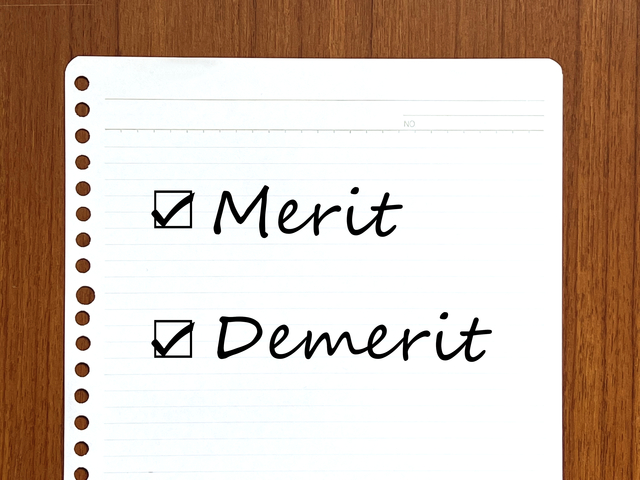
型彫り放電加工のメリット
型彫り放電加工には以下のようなメリットがあります。それぞれについて解説します。
- 硬度に関係なく加工できる
- 複雑な形状も加工できる
- 機械が壊れる可能性が低い
①硬度に関係なく加工できる
型彫り放電加工は、放電加工のため通電性がない材料には適応できませんが硬材や焼入材など材料の硬度が硬くても加工することができる技術です。
②複雑な形状も加工できる
型彫り放電加工は、導電性のある材料であれば非常に硬い材料や複雑な形状でも精度の高い製品に加工することができます。
③機械が壊れる可能性が低い
型彫り放電加工の機械は、対象の材料に、触れることがないためそれだけ壊れる可能性は低いといえます。
型彫り放電加工のデメリット
型彫り放電加工にはメリットだけでなく、以下のようなデメリットがあります。それぞれについて解説します。
- 導電性のない材料の加工はできない
- 1回の放電で削れる部分が少なく加工に時間がかかる
- 加工機械が高価
- 電極を材料に合わせて作る必要がある
①導電性のない材料の加工はできない
型彫り放電加工のデメリットに、導電性がない材料は加工できないことがあげられます。型彫り放電加工は導電性のある材料なら非常に硬い金属でも加工できますが逆に、導電性のない材料では加工することができません。
②1回の放電で削れる部分が少なく加工に時間がかかる
型彫り放電加工では一回の放電で削る部分が少なくなるため、どうしても加工に時間がかかり量産性はありません。
③加工機械が高価
かなり高値になり数十万円から高いもので、数百万円かかります。
④電極を材料に合わせて作る必要がある
型彫り放電加工では、加工液の中の細かな除去を繰り返し行うことで電極形状が反転された3次元形状に加工します。そのため、銅・タングステン・グラファイトなどの電極を、目的の材料に合わせて作る必要があります。また、切削加工によって電極の形状に整形しなくてはならず、余分な工程が増えてしまいます。
まとめ
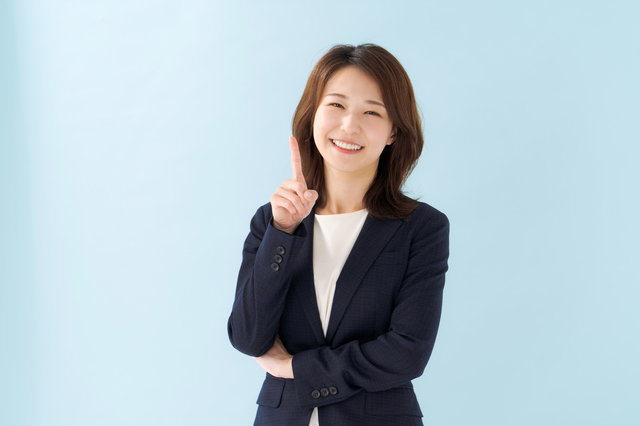
【型彫り放電加工とは】
油などの絶縁性のある加工液の中で、電極と材料を対面させ、微小な放電を何度も発生させて放電加工させる技術です。放電加工は切削加工と違い、導電性の材料なら、どんなに硬い金属でも加工することができます。また、精度の高い製品に加工することも可能で、切削加工などと違い材料に接触せずに加工できるため、機械が損傷する可能性は低いです。
【放電加工の種類】
- ワイヤー放電加工
- 型彫り放電加工
【形彫り放電加工とワイヤー放電加工との違い】
- 電極の違い
- 加工の仕方の違い
- 主な加工物の違い
【型彫り放電加工のメリット】
- 硬度に関係なく加工できる
- 複雑な形状も加工できる
- 機械が壊れる可能性が低い
【型彫り放電加工のデメリット】
- 導電性のない材料の加工はできない
- 1回の放電で削れる部分が少なく加工に時間がかかる
- 加工機械が高価
- 電極を材料に合わせて作る必要がある